Attache remorque de L'Incongrue
Introduction
L'Incongrue est un tiers lieu situé à Gieres (Isère). Le projet est de permettre aux villageois d'utiliser des remorques à vélo gratuitement. On a récupéré des remorques (et on compte en construire d'autres) mais il nous manque un système d'attache.
Contraintes
Les contraintes du projet sont les suivantes :
- Les remorques sont garées dans l'espace publique :
- Aucune pièce de l'attache ne doit pouvoir être retiré
- Il ne faut pas que l'attache rouille
- L'attache remorque doit rester sur la remorque
- Les utilisateurs n'ont pas de formation particulière ni d'équipement :
- L’accrochage de la remorque doit se faire sans outils
- La remorque doit pouvoir être attachée sur n'importe quel type de vélo
- L'attache remorque doit avoir 3 degrés de liberté :
- Tangage : quand on passe un dos d’âne, l'angle entre la remorque et le vélo change
- Roulis : lorsqu’on tourne en vélo, le vélo se penche. Mais ce n'est pas le cas de la remorque
- Lacet : Toujours en virage, un angle apparait entre le vélo et la remorque (d'autant plus à basse vitesse)
On a choisi de s'accrocher au tube de selle : C'est la seule partie du vélo facilement accessible avec un diamètre qui ne bouge pas trop. Pour ne pas marquer les tubes de selle (et pour que ça tienne bine), on utilise de la chambre à air.
Les pièces en métal seront en Inox. Pourquoi ?
- Trois solutions sont possibles : Acier, Inox, Acier galvanisé
- L'acier rouille et nécessite donc une opération supplémentaire de protection
- L'acier galvanisé est un acier recouvert d'une couche de zinc. Il ne rouille pas. Par contre, on ne peut pas le souder directement. (Les vapeurs sont très toxique et ça se soude très très mal). Il faut retirer la couche de zinc puis souder puis protéger les zone qui ont été décapées.
- L'Inox est plus cher, se perce moins bien mais se soude très facilement au TIG (comme l'acier). Les pièces de la rotule sont donc en inox mais on a conservé le galva pour la visserie qui sert a serrer la tige de selle.
Plan

Les plans sont disponible dans un Dépot Github
On trouve les documents suivants :
- Fichier source Freecad
- Plans :
- Pièces 3D :
Matériaux
Matériaux nécessaires :
- 2 X Vis M8x60
- 6 x Écrou M8
- 2 x Rondelle M8
- 2 x 30mm de chambre à air de route (15x18 ou 18x25)
- 200g de PLA ou PETG (pour la réalisation des pièces plastiques), on peut faire sans
- 6 Écrou M18 en Inox (On peut travailler avec de l'acier galva, bien moins cher, mais il faudra retirer la couche de zinc avant soudure puis protéger les zones décapées à la fin)
- 1 tige filetée M10 en Inox (Idem que pour les écrou : galva possible) : c'est dans ce morceau que trois éléments doivent être découpés :
- 1 x 30mm
- 1 x 36mm
- 1 morceau qui sera soudé sur la remorque
- 1 fer plat de 30mm*3mm en Inox (Idem que pour les écrou : galva possible). Découpé en trois parties :
- 1 x 30mmx30mm
- 2 x 80mmx30mm
- Un peu de fil électrique 1,5mm²
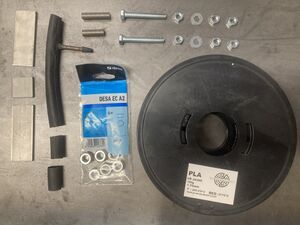
Cout de l'attache remorque : TODO
Outils
Liste des outils nécessaires :
- Poste TIG
- Perceuse à colonne (non présente sur la photo)
- Forêt 3mm, 8mm, 10mm. Un forêt étagé est une alternative bien pratique.
- Frein filet moyen (le bleu)
- Scie à métaux
- Équerre / Crayon / Pied à coulisse
- Pointeau + Marteau
- Lime
- Clé de 13
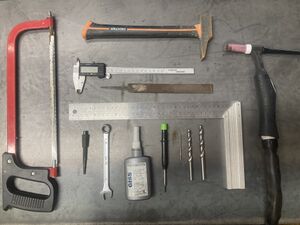
EPI
EPI nécessaires :
- Cagoule de soudage
- Gant de manutention
- Protection auditive
- Lunettes de protection
- Vêtements et chaussures adaptés

Préparation des plaques et vis
Vis
Pour s'assurer que les boutons ne pourront pas être désolidarisés de l'attache remorque, nous allons ajouter deux goupilles sur les vis. Cette étape est facultative si on désire garder l'attache remorque chez soi.
En premier lieu, on réalise un méplat à la lime sur le bout de la vis. Je n'ai pas mesuré mais je dirais sur 8mm. Avec le pointeau on marque l'emplacement du trou qu'on va réaliser :
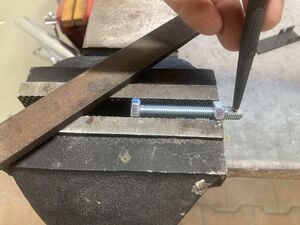
Ensuite, on réalise un perçage avec le foret de 3mm :
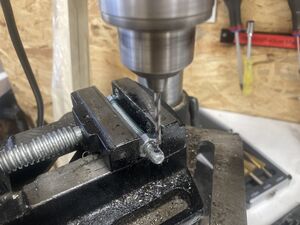
Les deux tiges filetées doivent être limées au centre (réalisation d'un méplat) :
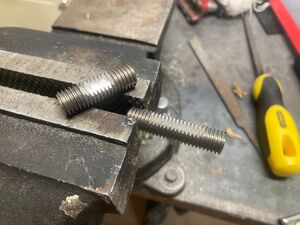
Plaques
Les 3 plaques réalisées dans le fer plat doivent être percées :
- La petite avec un trou de 12mm
- Une avec deux trous de 8mm séparées de 56mm
- La dernière avec deux trous de 10mm séparées aussi de 56mm
![]() |
![]() |
Sur la contreplaque, on scie pour lui permettre de de se mettre en place sur une vis. Une des découpes est perpendiculaire au bord, l'autre doit être faite avec un angle :
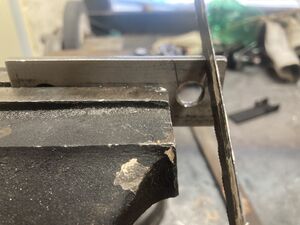
Une fois ébavurée et limée, la plaque :
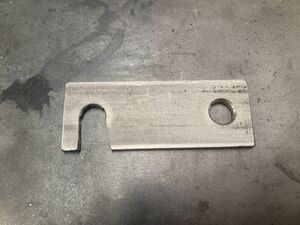
Écrous
Deux écrous doivent être percés au diamètre 10mm :
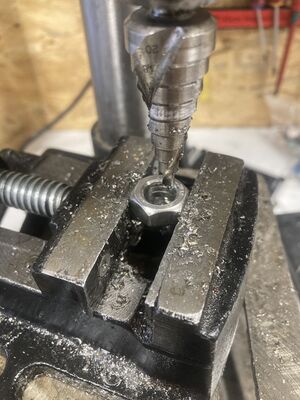
Impression des pièces plastiques
Cette section est facultative :
- Les boutons peuvent êtres remplacés par des écrous papillons
- Le bloc avec un demi tube retiré peut être réalisé en bois. Dans cas, il faut percer en D35
Pour la réalisation, nous avons utiliser du PLA mais il est possible d'utiliser n'importe quel autre plastique.On réalise les pièces avec un taux de remplissage de 100%, épaisseur de couche 0.2mm.
Pour les boutons : Une pause doit être ajoutée dans le gcode à la couche 9.6mm. On insérera les écrous dans les boutons à ce moment là :
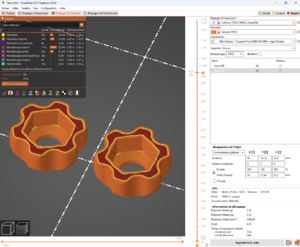
Les 3 pièces imprimées :
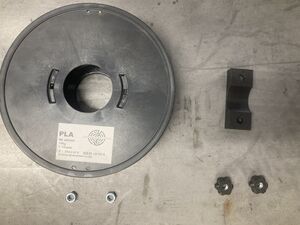
Chambre à air
Dans une vieille chambre à air 15x18, on découpe deux tronçons de 30mm. On insère ensuite un tronçon sur la pièce de plastique. C'est pas évident mais ça passe :
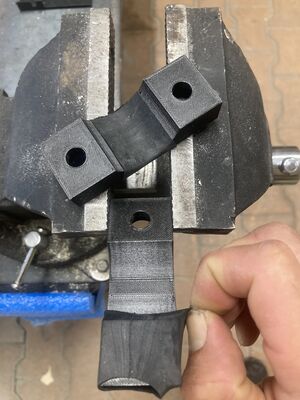
Le deuxième tronçon est mis autour de la contreplaque en métal :
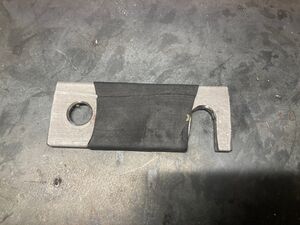
Soudure
Nous avons utilisé un poste à souder d'entrée de gamme. Réglage :
- DC, 70A, Argon : 8l/min.
- Préflow : 0.5s, Postflow : 2s
Les soudures sont toujours autogène (sans apport de matière). Mais parfois, on se sert d'une goutte de la baguette d'apport pour initier le point.
Première étape : un boulon M10 inox sur le plat de 30x30m :
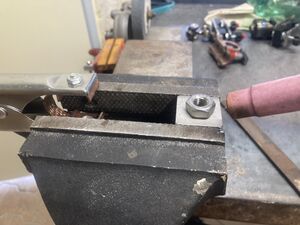
On pointe l'écrou 4/5 fois :
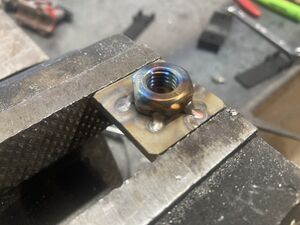
Sur la deuxième plaque, on positionne deux écrous qu'on pointe :

On ajoute ensuite l'écrou qu'on soude. Attention, la masse du TIG doit être positionnée sur la tige filetée :
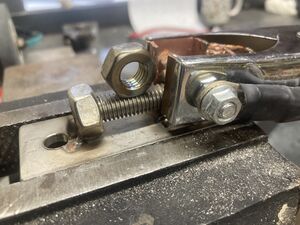
Soudure de la deuxième tige filetée :
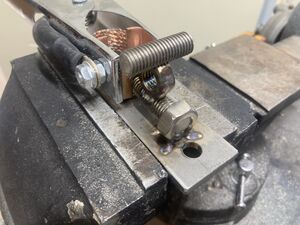
On met en place les deux derniers écrous M10 (dont un percé) et la plaque. On se débrouille pour que tout tienne plus ou moins en place et on pointe :

Ouf, la soudure est terminée.
Assemblage final
Mise en place des deux vis M8, frein filet et on serre en forçant un peu :
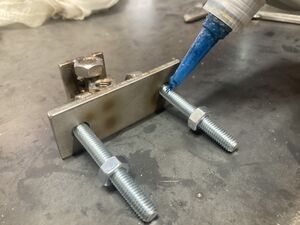
On met en place la pièce plastique, les deux rondelles, les deux écrous :
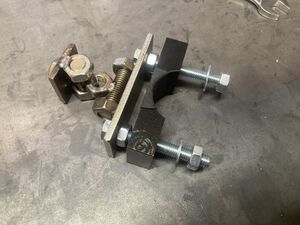
On ajoute le frein filet et on serre pas trop fort :

On prend un bout de fil électrique 1.5² et on s'en sert comme goupille :

Une fois le montage terminé :
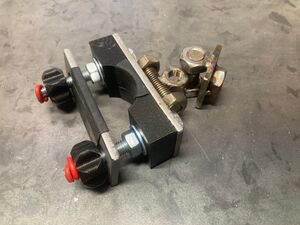
Conclusion
Les points qui peuvent poser problème :
- Perçage : on fini vite par bruler les forêts. Les conseils : vitesse de rotation lente (perso, je suis à 600tr/min et c'est beaucoup trop rapide pour du D10 dans l'Inox), et huile de coupe
- Soudage : Si on ne suit pas bien la procédure, on risque de gripper une des petites tige filetées dans les écrous M10. Il faut chauffer le moins possible les tiges filetées et que la masse du poste soit directement sur la tige filetée. Je me demande si on ne devrait pas utiliser du tube plein (avec goupille ou circlips), ça serait surement plus simple.
Autre réalisation avec un demi cardan :
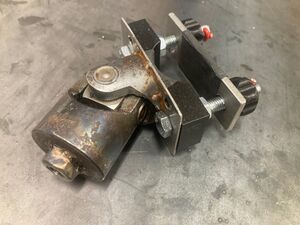